Product Categories
Product Tags
10 materials for CNC machining prototypes
Compared with 3D printing, the biggest advantage of CNC prototype is the richness and practicality of materials. The main purpose of the prototype is to verify the feasibility of the product design, so the materials of the prototype are also very particular. Each company’s products are different, and the prototype models that need to be made are also different. Therefore, the production materials may also be different, but the main processing materials include the following:
Compared with 3D printing, the biggest advantage of CNC prototype is the richness and practicality of materials. The main purpose of the prototype is to verify the feasibility of the product design, so the materials of the prototype are also very particular. Each company's products are different, and the prototype models that need to be made are also different. Therefore, the production materials may also be different, but the main processing materials include the following:
2. PC: Material with good strength, toughness and transparency, suitable for the production of Lens and fine structure parts. In addition, glass fiber is added to improve the steel and heat resistance of the board, which can be used to make parts that need to maintain high rigidity in a high temperature environment. PC also has UL94-V0 fire rating;
3. PMMA: Namely acrylic, or plexiglass. It is a good transparent part, the material with the best transparency can be made with surface treatment such as dyeing, electroplating, spraying, and screen printing. The welding strength is acceptable, but fragility is its weak point, and it is not suitable for use in vulnerable places such as hooks;
4. PP: Translucent material, good impact resistance, excellent flexibility, can be applied to products with strict impact resistance conditions. Such as: automotive supplies, half-folding packaging boxes, etc.
5. PA66+GF30: PA66+GF30 is not a model, it is a general code for PA66 plastic materials with 30% glass fiber. High strength, special thermal stability, hydrolysis resistance, suitable for auto parts, mechanical parts, etc. It is used as a shield for mechanical parts that require high rigidity and dimensional stability. Red phosphorus flame retardant has long-term stability and excellent mechanical processing performance;
6. POM: It is called polymethine raw material in Chinese, also known as polyoxymethine raw material. It is often called Saigang in the prototype industry. The regular molecular structure and crystallinity make its physical and mechanical properties very excellent, and it is called metal plastic. In the prototype model, it is suitable for high-strength workpieces, such as gears, shafts, brackets, etc.;
7. Teflon: The chemical name is polytetrafluoroethylene (PTFE for short), which is generally called "non-stick coating" or "easy to clean material". This material is resistant to acids, alkalis, and various organic solvents, and is almost insoluble in all solvents. At the same time, PTFE has the characteristics of high temperature resistance, and its friction coefficient is very low, so it can be used for lubrication and become an ideal coating for easy cleaning of the inner layer of water pipes;
8. Aluminum alloy: Aluminum alloy is the most widely used non-ferrous metal structural material in prototype models, and has been widely used in aviation, aerospace, automotive, medical, and ship prototype models. At present, aluminum alloy is the most used alloy in prototypes. The advantages are easy processing and forming, good rigidity, and rich anode coloring;
9. Magnesium alloy: light weight and good strength, it is a favorite material for consumer 3C. The disadvantage is that magnesium is a flammable metal, and environmental control is very important during machining. The manufacturing process of magnesium alloy model is highly dangerous, and there are many machining processes after die-casting during production, which is a high-cost application material;
10. Brass: Brass is an alloy composed of copper and zinc. Brass composed of copper and zinc is called ordinary brass. If it is a variety of alloys composed of two or more elements, it is called special brass. Brass has strong wear resistance. Brass is often used in prototype models to replace materials that are difficult to engrave and mill, such as stainless steel. After polishing and electroplating, the surface effect and feel are very close to stainless steel.
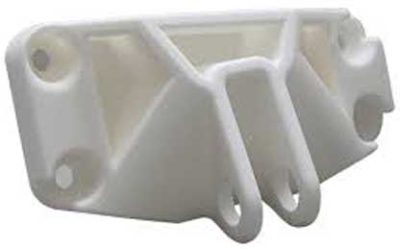
CNC machined ABS prototype
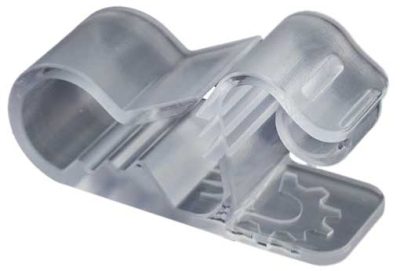
CNC machining PC prototype
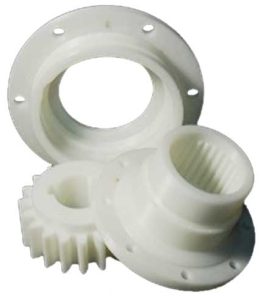
CNC machining PP rapid prototype
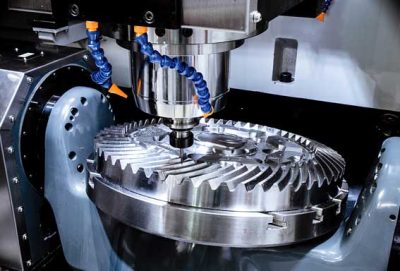
Aluminum alloy rapid prototyping
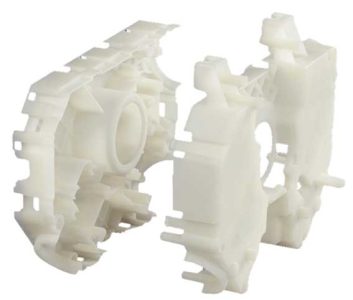
CNC machining POM rapid prototyping
Contact Us
Waiting for your email, we will reply you within 12 hours with valuable information you needed.